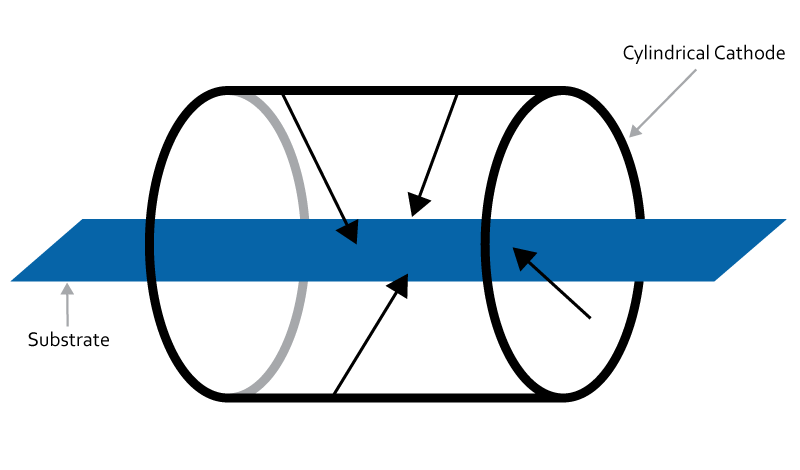
Posted on
An inverted cylindrical cathode configuration, compared to a planar or confocal configuration, has a few notable benefits because of its highly unique design. Unlike most cathode arrangements, where the cathodes sputter down, up or across the chamber, an inverted cylindrical cathode sputters inward toward the center of the cylinder. This offers several advantages for precision optics, biomedical and precious metal applications.
What is an Inverted Cylindrical Cathode?
An inverted cylindrical cathode is designed exactly as the name implies: it is shaped like a cylinder, with the target on a ring on the inside of the cathode. The substrate is placed inside the cylinder during deposition. The sputtering direction is inward, from the outer ring towards the substrate.
With this configuration, all sides of the substrate are coated at the same time. It’s a unique design offered only by Denton Vacuum that gives several advantages for certain applications.
Benefits of an Inverted Cylindrical Cathode Configuration
The main benefits of this type of cathode are:
- Excellent thickness uniformity: Good thickness uniformity is inherent in this design. This is particularly useful when depositing thin film coatings onto curved surfaces such as optical lenses and mirrors; a cylindrical cathode makes it possible to achieve uniform thickness across the curved surface without any complex motion or uniformity shaping.
- Ability to coat complex or 3D shapes: Uniformity is a big benefit for any type of substrate, but particularly for those with complex surfaces such as a stent. An inverted cylindrical cathode can help ensure that uniform coatings are deposited across the entire surface, even with a complex topography or unconventional substrate shape.
- High deposition rates: An inverted cylindrical cathode offers inherently high deposition rates so you don’t have to sacrifice production volume to achieve acceptable performance.
- Excellent target utilization: In other configurations, the sputtering process creates a racetrack-like groove on the cathode, which can greatly degrade target utilization. An inverted cylindrical cathode offers highly uniform erosion across the surface of the target, which may double or triple the amount of material you can sputter from a single target. This is especially important for applications requiring expensive target materials; a cylindrical cathode may help reduce cost of ownership for the entire system by reducing net target costs.
How an Inverted Cylindrical Cathode Meets Application Needs
The inverted cylindrical cathode design is a unique one, and the benefits it provides are inherently suited for specific applications. Here are some applications where inverted cylindrical cathodes during sputtering may make the most sense:
- Medical devices: Coatings for medical devices must meet very specific requirements and specs. Devices such as implants may have a complex shape or surface for coating; other devices, like stents, have curved surfaces that need to be coating uniformly. These coatings also need to be biocompatible. Inverted cylindrical cathodes are able to address all of these needs.
- Curved optics: Cylindrical cathode technology could have big implications for precision optics coaters. Normally, reaching exacting specs for these coatings means investing in a slower, more expensive process. An inverted cylindrical cathode can address some of these concerns, by offering high uniformity for curved surfaces alongside high deposition rates.
- Roll-to-roll precious metals: With greater efficiency in coating both sides at once and high target utilization, an inverted cylindrical cathode can dramatically reduce target costs. This is crucial to meeting cost of ownership requirements for applications using precious metals. To increase deposition rates, multiple cathodes can be employed in a single system to meet production requirements within a small footprint.
Denton Vacuum recently acquired the Isoflux cylindrical cathode portfolio, including equipment intellectual property and patents. This cathode is directly compatible with Denton’s Discovery 200 sputtering module, and our team of engineers can work with you to optimize your configuration for your unique application requirements.
If you have questions about whether an inverted cylindrical cathode is the right choice for your application needs, please contact us today.