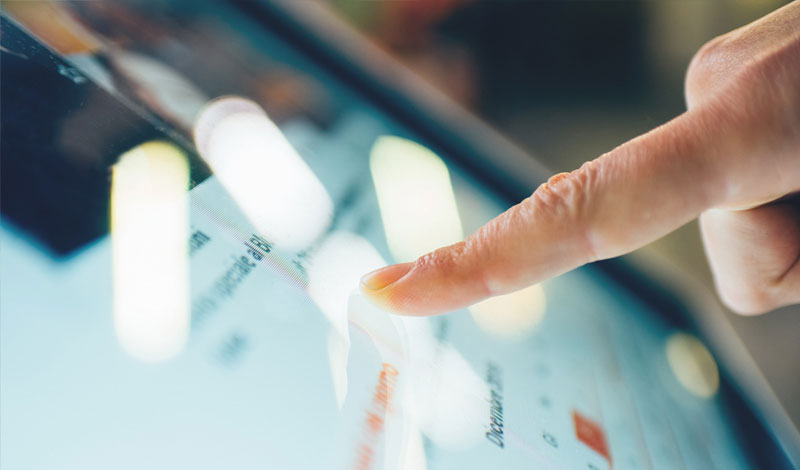
Posted on
Thin film coatings serve a number of purposes for different applications, including across the opto-electronics, display, semiconductor and medical fields. Here is a quick rundown of a number of common coatings that are available, their properties, and the applications they’re optimized for in order to help you figure out the best coating for your performance requirements.
AR/HR Coatings
Certain types of coatings are designed to change the way an optic interacts with light; two of these are antireflective and high reflectivity coatings (AR/HR). They interact with light waves in different ways, but both are used to meet specific performance requirements for optical, laser, and display applications.
Antireflective (AR) coatings increase the transmission of light in order to reduce surface reflections. They are commonly used on lenses and displays that demand little to no reflectivity, such as reducing glare from eyeglasses, eliminating reflected light effects in camera lenses, and improving collection efficiency of solar cells.
High reflectivity (HR) coatings are mirrors that decrease transmission to provide high surface reflectance. HR coatings reflect most or all light of a given wavelength range, and can be specified to provide the “right” amount of transmission for a particular application, such as the output mirror on a laser.
Both AR and HR coatings can be used in laser applications, depending on the performance specs needed and type of laser. To deposit AR/HR coatings onto an edge-emitting diode laser, either ion assisted deposition, sputtering or ion beam deposition can be used.
TCO Coatings
Transparent Conductive Oxide (TCO) is a type of inorganic transparent conductive film (TCT) that is used in electronics. TCO coatings are primarily used within the opto-electronics and display space. This type of thin film is electrically conductive and transparent, making it suitable for use in photovoltaics, LCDs, OLEDs, and touchscreens.
Indium tin oxide (ITO) is a type of TCO coating that possesses a high transmittance and low resistivity, but indium is becoming expensive as demand increases, so manufacturers are looking for alternatives. Many companies are investigating aluminum zinc oxide (AlZnO) as an alternate TCO material.
Common applications for TCO coatings include:
- Liquid crystal displays (LCDs)
- Plasma Screens
- Electronic ink applications
- LEDs
- Organic LEDs
- Touch screens
- Solar Cells / Photovoltaics
- Heated windscreens and mirrors
- Sensor coatings
- Strain gauges
For deposition of TCO coatings, magnetron sputtering is an ideal method for a cost-effective, high-volume solution.
DLC Coatings
Diamond-like carbon (DLC) coatings provide many of the same beneficial properties that are typical of diamonds: hardness, chemical and scratch resistance and lubricity. They also possess high thermal conductivity and electrical resistivity, and are most often used to increase the durability and lifespan of the end-use device or product.
DLC coatings are useful for:
- Microelectronics
- Medical devices
- Automotive components
- Displays
- Sensors
- Flexible semiconductors
PE-CVD (plasma-enhanced chemical vapor deposition) is one method for depositing DLC coatings. Its key advantages are high deposition rates, low substrate temperature, and highly conformal thin films.
Biocompatible Hard Coatings
As the name suggests, these types of coatings are used primarily in the medical field to protect implanted devices and improve health outcomes in this critical and sensitive market.
Biocompatible coatings are used on artificial limbs and joints, biosensors, and heart implants among other applications. They protect the human body and its tissue from contamination, as well as shield the device from exposure to proteins, glucose and cell adhesion. In doing so, they increase the durability of implants and similar devices.
Examples of biocompatible coatings include:
- Titanium nitride (TiN)
- Titanium aluminum nitride (TiAlN/AlTiN)
- Chrome nitride (CrN)
- Titanium carbo-nitride (TiCN)
For thin film deposition, magnetron sputtering can be used for conformal biocompatible hard coatings on 3D medical implants for wear resistance and color coding. Either PE-CVD or magnetron sputtering can be the deposition method of choice for TiN coatings, depending on the film property requirements.
Denton offers thin film deposition equipment for sputtering, PE-CVD, ion assisted deposition, and other methods to suit your specific application. Check out a full listing of our products and technologies here.