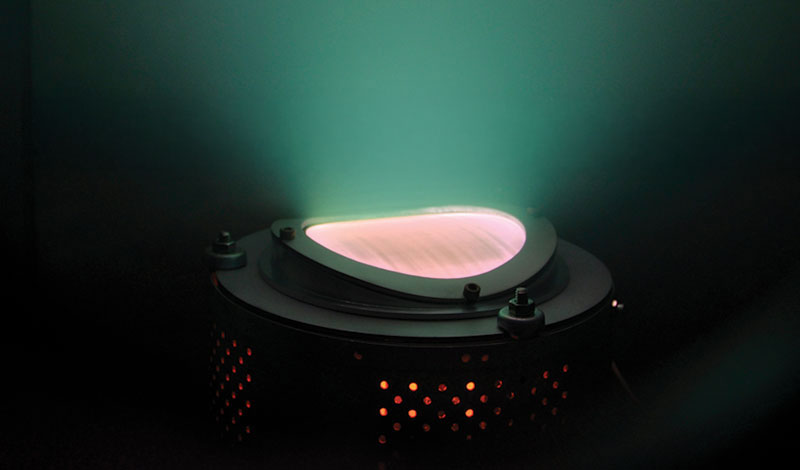
Posted on
Denton’s multiple system platforms and its proprietary thin film process technologies enable Denton to deliver unique solutions tailored to customers’ specific applications. In particular, Denton’s proprietary ion energy plasma technologies are uniquely capable of helping semiconductor and nanotech companies produce low-damage, contamination-free, shift-free, ultra-thin and uniform films.
Denton’s proprietary ion energy plasma technologies include:
- Endeavor RF Ion Source
- Endeavor Large Area Linear Ion Source
- Isoflux Cylindrical Magnetron
- Biased Target Sputtering (BTS)
Endeavor RF Ion Source
- Filament-free design, for lower maintenance and lower CoO
- Stable operation, for greater uptime and a higher yield
- Excellent stress control for better adhesion and higher yield
- Precise energy tunability for tight process control and higher yield
- Available on the Voyager PIB-CVD and the Integrity thin film deposition systems
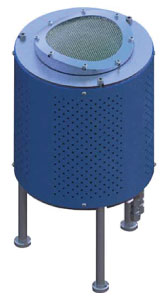
Denton’s Endeavor Circular RF Ion Source is designed to operate without a filament and uses a single extraction grid. Because the flux of electrons extracted from the source is sufficient to neutralize the ion beam space charge and eliminate space charge arcing in the chamber, this RF ion source does not require an auxiliary electron neutralizer, such as a hot-filament or hollow cathode.
The Endeavor ion source has enabled a new class of deposition called Plasma Ion Beam chemical vapor deposition (PIB-CVD). Because of the flexibility and tunability of the source design, it gets around many of the limitations of traditional plasma-enhanced chemical vapor deposition (PE-CVD).
The Endeavor circular ion source offers high current density and ion energy for optimal film densification and production of defect-free films. The tunable, independent control of ion energy and ion current density result in a wide process window that produces stress-free films for better adhesion and higher yield. As an RF ion source, the Endeavor offers the versatility of easily etching insulators and metals.
Designed for stable operation, the Endeavor ion source can operate continuously for more than 120 hours with no process drift. Its filament-free design avoids contamination and need for frequent filament changes, resulting in a longer Mean Time Between Planned Maintenance (MTBPM).
Its low ion energy mode can be used for pre-clean and plasma treatment without plasma damage.
The Integrity thin film deposition system is built for high-volume production. In addition to the filament-free Endeavor RF Ion Source, the Integrity system can also be configured for thermal and e-beam evaporation, provides high deposition rate, PID control, and excellent film crystallography. The Integrity is designed for demanding semiconductor, compound semiconductor, and optical applications.
The Endeavor Large Area Linear Ion Source
- Scalable, up to 3 meters
- Suitable for in-line continuous production
- Tunable
- Stable, designed for long process runs
- Available on the Phoenix PIB-CVD
The patented Endeavor Large Area Linear Ion Source is scalable up to a length of three meters. This makes it suitable for in-line continuous production or large drum batch systems.
Like the other Endeavor ion sources, it is tunable, enabling it to deposit materials with a wide range of properties even with a single precursor. The ion energy is controlled independent of plasma density by biasing of the source; as a result, there is no need for substrate biasing or high temperatures.
It is also stable, with an internal Inductively Couple Plasma (ICP) RF antenna that generates a high-density plasma. The RF generator is built around Denton’s proprietary match design for fast and automatic tuning. The biasing scheme is insensitive to dielectric build up on components, which enables long, stable production campaigns. No external neutralizer is required, avoiding the drawbacks of more typical “point source” neutralizers.
The Endeavor Large Area Linear ion source operates cleanly, with precursor gases injected via the process chamber rather than through the source. It is also easy to maintain.
The Phoenix PIB-CVD is based around Denton’s patented linear ion source, which enables a new class of thin film deposition called Plasma Ion Beam CVD (PIB-CVD). This deposition method can be tuned to produce coating compositions ranging from polymer-like to a diamond-like coating (DLC).
Linear RF Ion Source: Technology and Typical Geometry
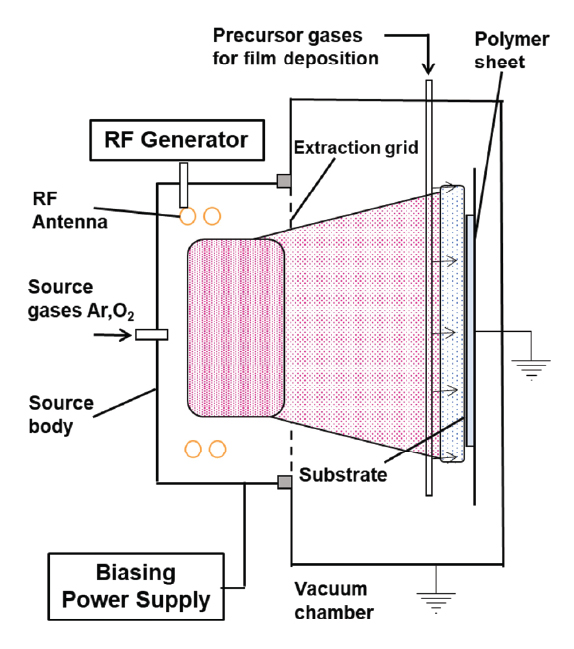
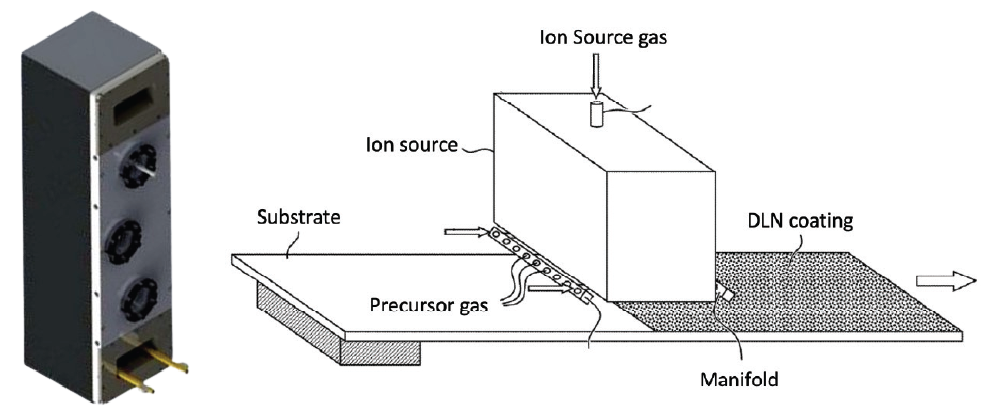
Linearized Energetic Radio-Frequency Plasma Ion Source (US Patent No. US 10,815,570 B2)
Denton PIB-CVD process has a wide range tunability of ion energy and ion current density eliminating the need for substrate biasing.
The benefit of this geometry is large area coating and is possible due to no need for substrate biasing. Roll-to-roll coating is hard to implement with substrate biasing.
Isoflux Cylindrical Magnetron
- High uniformity and repeatability
- Handles curved, 3D, and complex substrates
- High-energy plasmas
- High deposition rates
- Excellent utilization of expensive materials
- Available on the Discovery Isoflux
The Isoflux Inverted Cylindrical Magnetron (ICM) is a great option for sputtering applications that require uniform coatings on curved, 3D or complex substrates. ICM sputtering follows the same steps as conventional magnetron sputtering except a cylindrical cathode is used instead of a planar cathode. Instead of sputtering up or down, the cylindrical cathode sputters inward.
ICM sputtering offers the repeatability needed for precision optics and delivers a more streamlined process for coating lens and other curved surfaces. Typically, rotation or planetary movement are needed to ensure all sides are coated, but this slows down the process and makes for a complicated coating process. By sputtering the entire surface at once, ICM sputtering reduces complexity while achieving tighter uniformity and control.
Along with precision optics, ICM sputtering also offers very high thickness uniformity (+/- 0.25%) for medical device coatings, such as implants. Reliability is critical for these applications in order to protect patient safety. ICM sputtering is a good solution for achieving tight coating specs and can also help increase radiopacity of a device.
With inherently high deposition rates, ICM sputtering also ensures production volume and ROI don’t have to be sacrificed to achieve high performance. This sputtering configuration can help lower cost of ownership as well, particularly in applications requiring expensive target materials. An inverted cylindrical cathode delivers highly uniform erosion across the surface of the target, improving target utilization for the entire system.
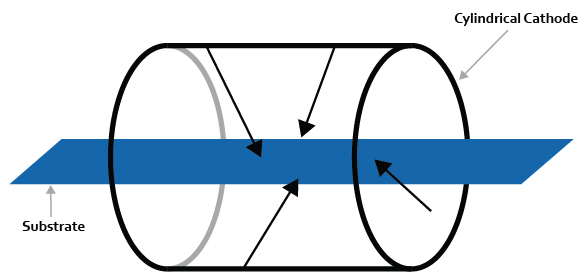
Biased Target Sputtering (BTS)
- No beam overspill, eliminating contamination or process particles
- Excellent stress control for better adhesion and higher yield
- Tight energy control for less plasma damage and higher yield
- Creates dense, defect-free, and shift-free films
- Available as an option on the Infinity Ion Beam Deposition system
While traditional Ion Beam Sputtering (IBS) systems provide good process control, there are drawbacks for certain applications. Denton’s patented Biased Target Sputtering (BTS) can overcome many of the well-known process issues of IBS, such as particulate contamination from system components and shields.
In contrast to the high-energy ions typical of IBS, BTS uses low-energy ions, below the sputter threshold, preventing particulate contamination. A negative voltage is applied to the target, creating a plasma sheath near the target that accelerates the ions in a way that enables sputtering from the target only. This eliminates contamination and scatter from beam overspill, enables tight stress control, and creates dense, defect-free films. In BTS, high-energy ions can only sputter the target, and these systems potentially have shorter source-to-target distance, allowing for a smaller footprint. BTS also achieves excellent uniformity on large substrates without requiring rotation, helping optimize overall manufacturing processes.
BTS can also be configured for Co-Sputtering of two target materials at the same time.
The ultralow contamination offered by BTS, its graduated energy process, and its tighter energy control make BTS ideal for applications such as:
- AR and HR Coatings for Edge-Emitting Lasers and VCSELs
- High-Quality VOx IR Absorbers for Microbolometers
- EUV Lithography (Extreme UV) Mask Blanks
Denton’s Infinity Ion Beam Deposition system with the Biased Target Sputtering (BTS) module offers independent control over ion currents and energies and operates at a low pressure to provide excellent control of thin film interfaces.
Biased Target Sputtering

Denton, the World Leader in Plasma Ion Energy Control
Denton Vacuum’s patented and proprietary technologies provide tremendous control over the levels of ion energy and ion current density separately from the power level set on the plasma or ion source power supply. This enables the design of novel films with a wide range of physical, mechanical, and compositional properties. Ultimately, this means more control of stress, composition, temperature, contamination, and alloying in thin film applications.
Conclusion
If you are interested in learning more about how Denton’s advanced thin film technologies and innovations can be applied to your processes, contact us today to discuss your particular needs.