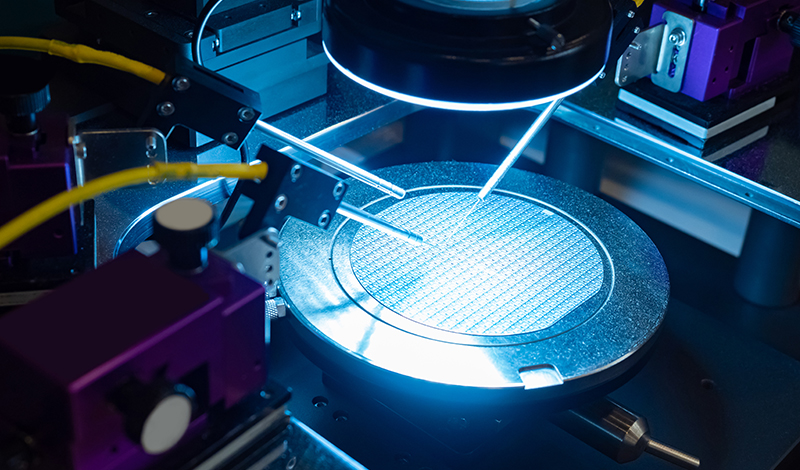
Posted on
In the intricate world of semiconductor manufacturing, understanding device failures and maintaining consistent quality is more than a technical challenge – it’s a critical business strategy. The smallest of quality issues can snowball to have an outsized impact on yield and profitability. Denton’s Infinity FA system can create automated, repeatable Failure Analysis (FA) and inline Quality Assurance (QA) processes, transforming how manufacturers detect, diagnose, and prevent production issues.
Semiconductor production is inherently complex. Manufacturers constantly wrestle with maintaining yield, preventing defects, and understanding why chips fail. Traditional methods have relied heavily on manual trial-and-error and post-production analysis, processes that are time-consuming, expensive, and prone to human error.
The Precision and Accuracy of the Infinity FA makes Automation Possible
The broad ion beam of the Infinity FA provides uniform delayering to expose large areas of interest (AOI) while maintaining damage-free layer removal. It employs various techniques to control the accurate removal of micrometer and nanometer levels of surface material while producing a flat, planar surface. Because it is a low-energy etch (only a few hundred eVs), the Infinity FA does not damage the underlying devices, enabling electrical tests.
The uniformity of the etch rate and the precision and accuracy of the Infinity FA – combined with its Secondary Ion Mass Spectrometry (SIMS) module to identify when a layer of interest has been reached – allows precise endpointing. The SIMS automated spectroscopy monitors the composition of the material removed, stopping etching once a pre-set signal has been reached. This makes it possible to create highly repeatable recipes that can be easily automated. The engineers in Denton’s application lab can help develop the optimal recipe.
Adding an automated feed rounds out the ability to automate much, if not all, of the QA and FA processes. Denton’s load lock, cassette load lock, and cluster load lock front-ends support scalable, high-throughput, automated processing for demanding, high-volume applications.
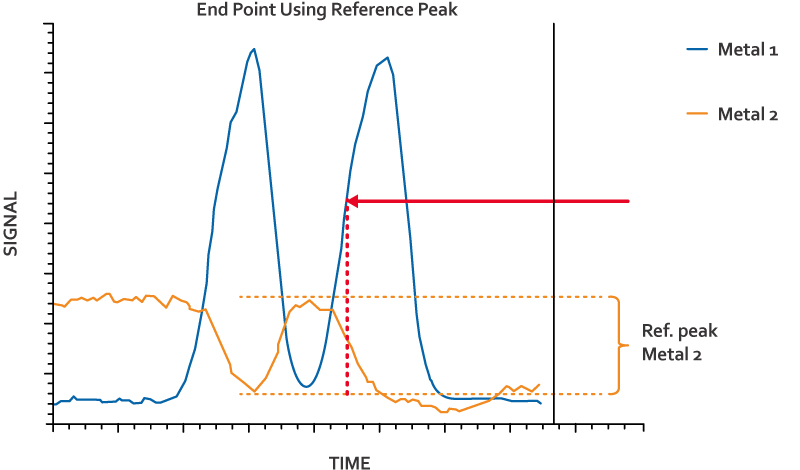
Inline QA: Real-Time Process Control
Inline Quality Assurance, where the Infinity FA system is tightly integrated into the manufacturing process, represents a proactive approach to manufacturing. By implementing real-time statistical process control, manufacturers can now detect subtle process variations immediately, adjust upstream manufacturing steps in real-time, prevent quality issues before they impact production, and minimize waste.
Semiconductor fabs are usually lights-out facilities. The fabs are automated to such an extent that there are no humans physically supervising the process, so lights are unnecessary. Humans are expensive. For the QA process to be integrated inline with the fab, it cannot be a manual process. The Infinity FA, combined with Denton’s Versa cluster platform, can make this possible.
The Role of Automated Failure Analysis
Automated Failure Analysis with the Infinity FA complements inline QA by providing deep, systematic insights into device performance.
When a chip fails a QA process – it didn’t calculate correctly, the transistors didn’t work, the pin outs aren’t correct – manufacturers conduct a detailed post-mortem to determine the cause. This process happens off-line, in a lab, and it inherently requires human intervention.
Using traditional FA techniques, the process is more of an art than a science. Manual polishing requires skill and finesse to work through the different layers, and chemical-mechanical planarization (CMP) requires experience in finding which chemicals work best to delayer the parts. It can be a life’s work to become expert at these techniques. It’s not only manual, it is mentally intensive work.
The uniformity of the etch rate and the precision and accuracy of the Infinity FA make it possible to automate much of the work involved in delayering a chip. There may still work to do, optimizing the system, but it’s different work. Instead of a completely manual and mentally intensive process, operators would be systematically optimizing a recipe-driven repeatable solution, adjusting etch angles and etch rates while monitoring the SIMS.
The technology behind the Infinity FA enables consistent, repeatable analysis processes, allows examination of multiple chips simultaneously, reduces reliance on expensive specialized expertise, and accelerates the identification of manufacturing anomalies.
For semiconductor manufacturers, these approaches offer significant economic and operational advantages. Enhanced yield management, reduced production costs, faster time-to-market, and more consistent product quality are now achievable with a sophisticated Infinity FA system that automates as much of the process as possible.
Economic and Operational Impact
Automated Failure Analysis and inline QA represent more than technological upgrades—they’re fundamental shifts in manufacturing philosophy. By providing faster, more consistent insights, these approaches are helping manufacturers innovate more efficiently and produce higher-quality devices.
The future of semiconductor manufacturing is automated, precise, and increasingly intelligent. As technologies continue to evolve, the ability to quickly diagnose, understand, and prevent device failures will become a critical competitive advantage.
To explore how Denton’s Infinity FA system might help transform your FA and QA processes, contact us today.