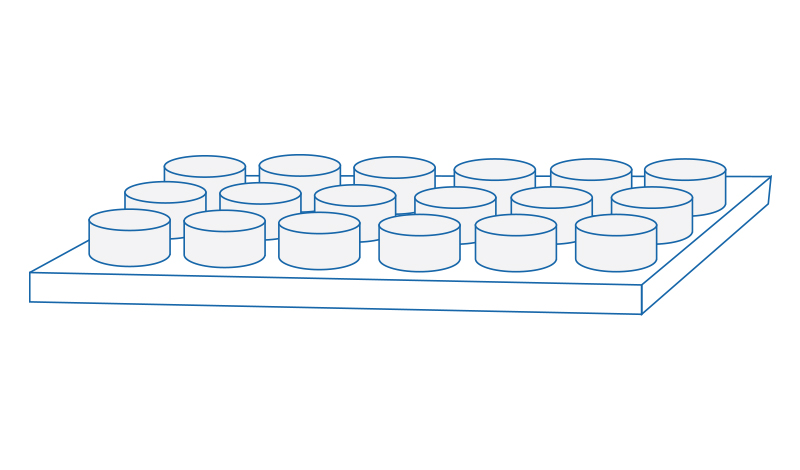
Posted on
With today’s technological advances, higher pixel density in focal plane arrays is a necessity as demand for improved visual quality goes up. Because of this, feature sizes on focal plane arrays are getting smaller, which requires higher density interconnects to bond the detector array to the readout chip. The current electroplating process just can’t deliver on high density pixels. Thin film deposition provides a better solution with optimized lift-off for more productive yields.
Crucial Indium Bump Components
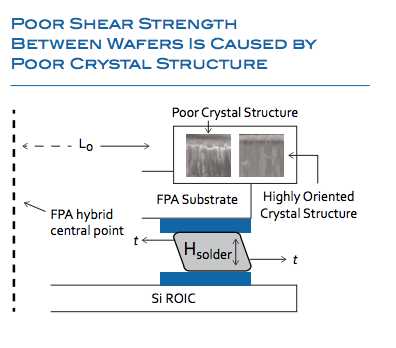
Two elements of focal plane arrays that are crucial to performance are shear strength and crystal structure. Generally speaking, shear strength can be defined as “the maximum shear load a body can withstand before failure occurs divided by its cross sectional area.”¹ In indium bump deposition, shear strength is essentially the degree to which the wafers and bumps can resist shear so that they don’t tear.
Crystal structure, or the makeup of the deposit between bumps, is what ensures that the shear strength is dependable. If the crystal structure is compromised anywhere, it will weaken the shear strength of the entire array.
Factors Impacting Crystal Structure
During the indium bump deposition process, geometry and temperature can both have significant impacts on the resulting crystal structure.
Geometry is important for ensuring direct deposition of the coating material. You need a deposition system that provides tight collimation control, in order to create a 7° maximum deviation from the direct line of sight. This enables the target to be hit directly, improving indium fill and enabling a high yield lift-off.
Temperature should also be closely controlled so that the crystal structure is not negatively impacted. The substrate stage needs to be cooled, so that it’s not too warm for indium’s low melting point of 156.6° C.
A cooled substrate stage and tight collimation control throughout the deposition process will help create excellent crystal structure with productive yields. A good crystal structure will raise the shear strength of the focal plane arrays, and by controlling these important factors through indium bump deposition, you’ll end with a more dependable, high-quality design.
For a deeper look at these factors and the indium bump deposition process, download our infographic, “3 Considerations for Indium Bump Deposition”.
¹ https://www.azom.com/article.aspx?ArticleID=3426#_Shear_Strength