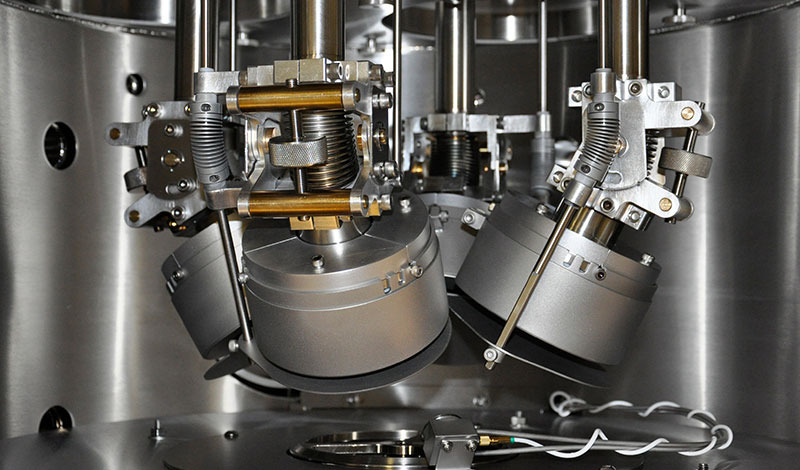
Posted on
There are several common types of thin film deposition techniques, with varying benefits depending on the method. But it’s not just the method that matters. Deposition source placement is one factor that can have a significant effect on thin film deposition. For sputtering, different cathode placement options can lead to different results for the thin film coating.
Sputtering as the PVD Method
In general, sputtering often achieves denser coatings than thermal evaporation or e-beam evaporation, because of the difference in the vaporization technique. With either of the evaporation methods, a source material is thermally evaporated inside a chamber or crucible and eventually deposits onto a substrate. In sputter deposition, however, the source material is ejected by magnetically confined gas ions colliding with the surface of the target. The ejected (or “sputtered”) material tends to have higher energy compared to evaporated material, which leads to denser films.
In sputtering, cathode placement can allow for better control over film thickness uniformity, giving this method yet another advantage. With confocal sputtering, multiple cathodes are placed so that they are equidistant and tangent to a circle that is parallel to the substrate. Using this method, the target size in some instances can be one half the diameter of the substrate, so target efficiency is another benefit. Because of these cathode placement options, sputter deposition can have a positive impact on yield and precision.
Options for Cathode Placement in Confocal Sputtering
There are a few different options for orientation of the cathode, each of which has their own advantages:
- A target larger than the substrate mounted directly above the substrate
- Cathodes with rotating magnets
- Rastering a substrate under rectangular cathodes
- Multiple cathodes mounted confocally around a single substrate
Benefits of Cathode Placement Options
Using either a target larger than the substrate mounted directly above it or using cathodes with rotating magnets will help improve the deposited thin film uniformity, so these are good considerations for when a very specific film distribution is needed. Cathodes with rotating magnets also help with target utilization, and rectangular cathodes are particularly useful for large area coating and high throughput.
There can be some limitations to all three of these approaches, however. When using multiple materials to deposit onto a substrate, the target must be changed after every deposition, which makes co-sputtering virtually impossible. You’re unable to simultaneously deposit more than one material.
If co-sputtering is a necessity, it may be worthwhile to consider confocally mounting multiple cathodes around a single substrate. Doing so allows you to deposit different materials in multiple layers onto the substrate at the same time, without having to change targets or break vacuum.
With confocal positioning to the substrate, the outer area of the substrate receives more coating material than the inner areas. Rotating the substrate around its own axis eliminates this non-uniformity, so you won’t lose the advantage of film uniformity even if you need to use the confocal method to achieve co-sputtering.
In our technical paper “Contributing Factors in Cathode Placement for Confocal Sputtering”, we take a deeper look at the benefits of confocal sputtering and the possibilities of co-sputtering within a single vacuum chamber. Download the paper here.