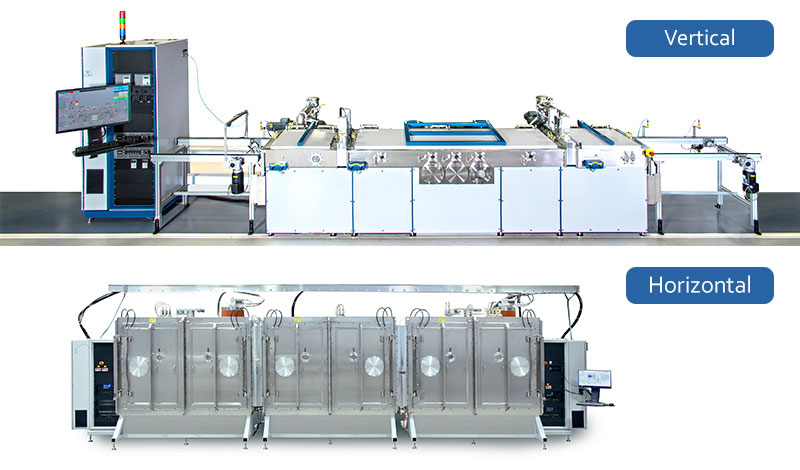
Posted on
One design consideration that can affect your process and thin film coating performance is the collective orientation of the substrate and cathodes during magnetron sputtering. Your system configuration may be oriented either horizontally or vertically, and both orientations have their benefits and tradeoffs.
Vertical Sputtering: Benefits
In a vertical sputtering configuration, the substrate and cathodes are positioned horizontally, and the sputtering direction is vertical. The process can be either sputter up or sputter down. In sputter up, the substrate sits above the cathodes, and the sputtering direction is upwards; sputter down is the opposite, with the substrate sitting below the cathodes and the sputtering direction going downwards.
Vertical sputtering is the process of choice across the board in compound semiconductor production, especially at high volumes. This type of configuration is compatible with off-the-shelf automation tools and front-end options, like load locks and cluster architectures, so if your process requires any automation this would be the right design for your system.
With a vertical configuration, one other benefit is that gravity can act as a clamp to hold the substrate in place. You’ll get a better edge exclusion because of this. Electrostatic chucks are commonly used as fixtures in vertical sputtering for compound semi applications, because they offer good heat transfer and help prevent warping of the substrate.
Certain applications require a very large target. You might need to use tiles of targets to meet this requirement, but for processes where the temperature inside the chamber is very hot, you can’t use indium to bond them because it will surpass its melting point. In such cases, you can make use of a vertical configuration to sputter up and eliminate the need for bonding the tiles.
Vertical Sputtering: Drawbacks
There are two main disadvantages with a vertical configuration: there is a risk that particles from flaking shields will fall onto the substrate during deposition, and for large substrates that are difficult to support it can be hard to keep the substrates flat during deposition.
In a sputter-down configuration particles may flake off and fall onto the substrate due to gravity. Even in a sputter-up configuration, these same particles may still drop down and land on your cathodes, causing an arc (and particles). This is best addressed by proper shield design and following a consistent preventive maintenance schedule.
Lack of flatness for large area substrates (typically made out of materials like glass or stainless steel) occurs because of the effects of gravity. When sagging or warping occurs, it presents issues with uncontrolled stress or cooling and possibly thickness uniformity, lowering your overall yield and your ROI.
Horizontal Sputtering: Benefits
In a horizontal configuration, the substrate and cathodes stand up vertically in the chamber, and the sputtering direction is horizontal. One benefit of a horizontal setup is that you may have to worry less about flaking particles. Because of gravity, particles will tend to fall to the bottom of the chamber, instead of on your cathodes or substrate. However, this does not eliminate the need for proper shield design and PM procedures – the best way to keep particles off your substrates is to keep them on your shields.
Gravity in a horizontal configuration also helps prevent the chance of sag in the substrates, because they aren’t laying flat. Addressing both of these concerns can improve your yield, as well as thin film coating performance and uniformity.
There are some mechanical benefits to a horizontal configuration that could help with loading the chamber as well. For very large substrates, such as glass or stainless steel panels, it’s easier to simply hang them with fixturing inside the chamber.
Horizontal Sputtering: Drawbacks
While horizontal sputtering may address a couple of process concerns, it isn’t an option for every application or substrate. Fixturing or clamping is a basic requirement for a horizontal configuration, to keep the substrates in place and standing up. Unfortunately, you will get some edge effect with that, because you won’t be able to go all the way to the edge of the substrate with the deposition.
Horizontal designs are also not suitable for a cluster architecture or standard semiconductor-type automation, so for high-volume production, you’ll need to stick with a vertical configuration that is compatible with such a system. And any application that requires substrate cooling will be easier to manage in a vertical configuration.
Denton Vacuum designs thin film deposition systems that can be configured either horizontally or vertically to suit your specific process and application needs. Contact us with any questions about these particular sputtering system designs.