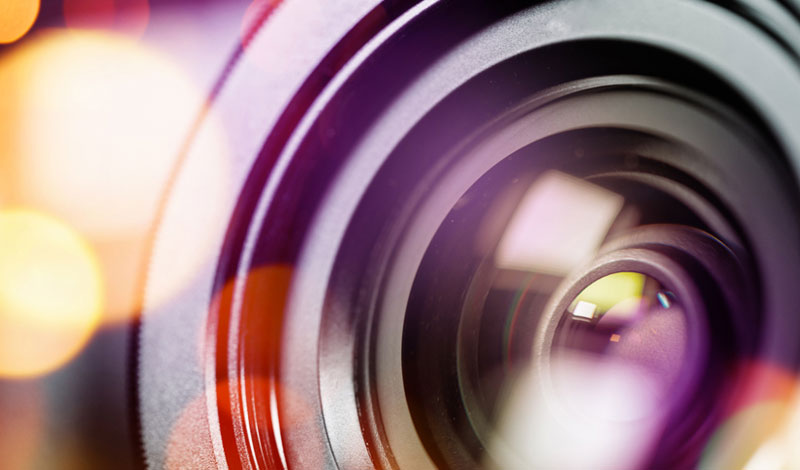
Posted on
Whether it’s coating a semiconductor chip with a protective thin film or applying anti-reflective coating to an eyeglass lens, process engineers have to achieve certain thickness specifications to meet performance requirements. Equally as important as the film thickness itself is the uniformity of the thickness.
Achieving Uniformity for Performance Specs
Without achieving proper thickness distribution, it can be difficult to ensure that the specifications are going to be fully met. The coating may meet thickness requirements on certain areas of the substrate, but if it’s not uniformly applied, other areas will be too thick or too thin and may not meet the performance requirements. For example, a large area anti-reflection coating would have different reflectivities at different points on the substrate, which would likely have an impact on overall performance.
Uniformity is necessary to meet performance specs in any application, regardless of deposition method. You might require a very fine film coating, and if it’s a little too thick in certain areas, it can have a negative effect on performance. And some substrates feature intricate topography, such as steps and vias, but still require even distribution (p. 113-14) to prevent unwanted cracks and possible device failure. Thickness uniformity is key, from impacts as trivial as the distortion of a mirror image all the way to the life-changing effects of a hip replacement not properly reinforced against wear and degradation.
Benefits Beyond Performance
But performance isn’t the only concern for process engineers. Other production factors are also helped by achieving uniformity, such as repeatability and yield rates. Film thickness uniformity provides confidence that specs are being met and there won’t be fluctuation in thickness from product to product. If you’re using a method or machine that delivers on uniformity, you can be sure the process will deliver high yield.
Achieving uniform, repeatable thickness distributions, however, is not enough to guarantee a viable process. Cost and uptime must also be considered. A BYU professor of physics noted (p. 110) that uniformity can be improved by increasing the distance between the source and substrate during deposition, but that “this is wasteful of evaporant.” A well-designed product will provide repeatable, uniform films while minimizing wasted material.
Thin film thickness uniformity is important to the deposition process in every application. It can affect a wide range of specs, from performance results to production yields and costs. You’ll lower your total cost of ownership by keeping your yield and repeatability on target and ensuring optimum performance is met.
If you’re wondering how you can achieve thickness uniformity for your thin film deposition application, we’ve studied the correct geometry needed for the production of uniform-thickness coatings. Read our findings by downloading the technical paper: Thickness Distribution of Evaporated Films.