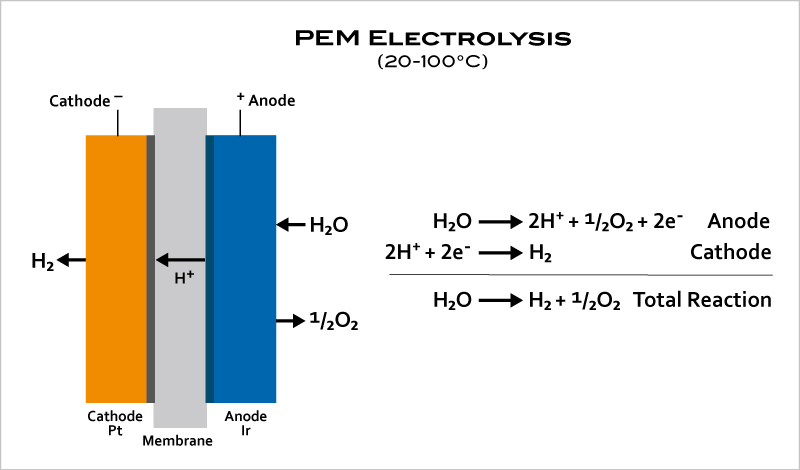
Posted on
One device helping make the carbon-free future more of a reality is the electrolyzer. Hydrogen is emerging as an increasingly important fuel source, and electrolyzers use electricity to perform electrolysis – the process of dividing water molecules into their separate components of hydrogen gas and oxygen gas. The oxygen and hydrogen can then be compressed and stored for later use.
Because electrolyzers use electricity, using a renewable energy source such as solar or wind power means the production of hydrogen can be done without releasing carbon dioxide into the atmosphere. They can be used in energy storage by converting excess electricity from such renewable energy sources into hydrogen gas. Such “green hydrogen” promises to be a critical enabler for the carbon neutral economy, in such applications such as fuel cell vehicles and hydrogen-enabled power plants.
3 Types of Electrolyzers
There are three common types of electrolyzers: alkaline, solid oxide, and polymer electrolyte membrane (PEM). Each type has its own method and design to produce hydrogen through electrolysis.
- Alkaline electrolyzers use a potassium hydroxide solution and two electrodes to separate hydrogen and oxygen.
- Solid oxide operates at relatively high temperatures (>700°C), which makes the efficiency very high.
- In PEM (acidic) electrolyzers, instead of an aqueous solution, the electrolyte is a thin, solid ion-conducting membrane to produce extremely pure hydrogen. PEM electrolyzers can operate effectively at high current densities and variable power levels, responding within seconds, making them a good match for renewable energy sources.
Electrolyzers can range from the size of home appliances or shipping containers, on the smaller end, to large-scale central production facilities that can supply trucks and pipelines on the larger end.
The Importance of Platinum in Electrolyzers
Titanium plates are used as the catalyst in PEM electrolyzers because they are corrosion-resistant, making them excellent for electrolysis cells. A platinum coating to the titanium substrate adds additional protection, and platinum’s catalytic properties significantly accelerate reaction rates, chemical transformations, electrolysis performance, and productivity.
Platinum-coated porous titanium plates play an important role in maintaining uniform current dispersion across the electrode cell. Porosity facilitates an even current flow and reduces the likelihood of hotspots or inconsistent reactions. Platinum coatings have traditionally been applied using rack plating or barrel plating. Both methods require submerging the plates in electroplating baths, a time-consuming process, and result in unused, waste platinum.
Platinum is expensive, making it the greatest variable cost for manufacturing electrolyzers when compared to labor and other expenses. But platinum is the optimal coating for electrolyzers to efficiently catalyze reactions, maintain greater reliability, and become cost effective for hydrogen production. This makes it critical for manufacturers to utilize platinum as efficiently as possible.
The Advantages of Thin Film Deposition for Platinum Coating
To optimize platinum use and apply the precious metal as efficiently as possible, electrolyzer manufacturers should consider thin film deposition methods. Thin film deposition systems utilizing plasma ion beam assisted deposition can deposit platinum coating to the titanium plates with exceptional precision, uniformity, and repeatability. Thin film deposition also enables use of a thinner platinum layer, using less platinum and reducing material costs.
If you’re interested in a thin film deposition solution for your application, consider Denton’s Phoenix large area coating system. The system enables high-volume deposition with efficient use of precious metals.