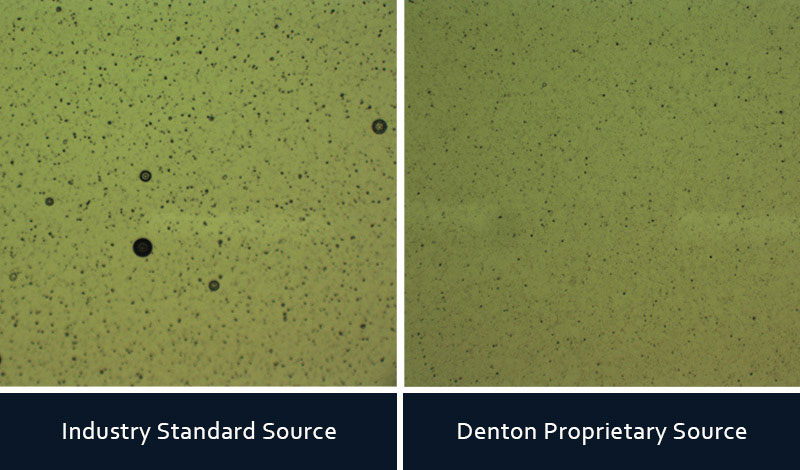
Posted on
Spit defects are some of the biggest obstacles to ensuring thickness uniformity and production efficiency in evaporation and indium bump deposition. There are ways to adjust your process to eliminate spit defects and improve yield, but if you work with a partner who has solved for these defects in their system design, you will realize a more efficient process and better performance over time.
What is “Spit” in Physical Vapor Deposition?
Spit refers to larger particles of the target material that are ejected from the source during evaporation. Normally, the material is smoothly and consistently evaporated from the source onto the substrate, to create a uniform coating or precise bump array.
Unlike these evaporated molecules, spits are large particles that solidify on the substrate surface and become embedded in the film coating, which can lead to performance issues. Spit defects need to be accounted for in your system design, otherwise they will create inefficiencies in your process.
Challenges of Spit Defects
The goal of any evaporation method is to create a coating on the substrate with the same thickness uniformity across the entire surface. Spit particles disrupt that uniformity, which degrades performance and reliability.
In indium bump deposition in particular, spit defects can have a negative impact on bump array yield. They can reduce the deposition into the vias that form the bumps, which can cause a low bump height. They may even be large enough to cover the via entirely, completely preventing bump formation. Since these spit defects will lead to defects and unreliable performance in real-world devices and applications, arrays that are impacted by spit particles will need to be partially or completely scrapped following deposition.
This can have a notable effect on your ROI. Since the bump deposition is one of the last steps in the process, you will be scrapping nearly complete components. This is the worst place to have a yield issue in terms of cost of ownership, because you are scrapping components when they have the most value.
Managing Spit Defects
It is possible to reduce or eliminate spit during evaporation by lowering the deposition rate. In thermal evaporation, a faster deposition rate causes more particles to uncontrollably eject from the source, instead of smoothly evaporating onto the substrate.
However, if you slow your deposition rate down too much, you will not have a very efficient process. There is a tradeoff here that you need to consider, because slowing the deposition rate means you will need to invest more in capital equipment to meet production demands, which drives up total production costs.
When you invest in a system that is intentionally designed to be spit-free, however, you are able to ensure uniform, reliable coatings without slowing your deposition rate down. A thin film deposition partner with deep process knowledge and experience handling spit defects will inherently manage that tradeoff for you.
The right configuration will account for spit defects in the actual evaporation system design, so you do not have to completely sacrifice deposition rate for thickness uniformity and bump array yield. When you need to constantly juggle these factors, it becomes difficult to gain process control for the long term.
Denton Vacuum is the market leader in indium bump applications, and we continuously invest in optimizing system design to account for spit defects. Our application-specific approach means that you will get a spit-free configuration without needing to lower your deposition rate, helping you meet production needs and gain tighter process control.
We are constantly using our experience with these applications to improve system design, and you can leverage that knowledge to ensure your own process meets key requirements for performance and production over time. Contact us to learn about solutions for your application.