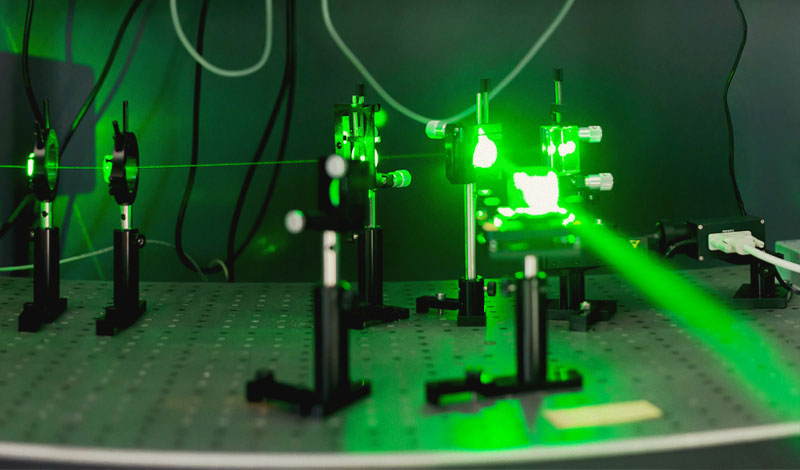
Posted on
Achieve improved system performance for thin film deposition in semiconductor laser manufacturing by optimizing your process flow.
The semiconductor laser market has seen phenomenal growth over the past 20 years, with diode lasers, largely driven by the fiber optics revolution, comprising around 45% of the $11B laser market. While growing, the semiconductor laser market is still relatively small in relation to the entire semiconductor market (around $350B).
Recently, the semiconductor market has established an industry-wide roadmap for production technologies, to prevent duplicate effort and investment. However, semiconductor laser fabs all use different toolsets and processes to reach similar goals, and process information is often closely guarded, as trade secrets.
Even with significant differences in scale, many of the leading semiconductor laser equipment vendors have adopted relevant practices from large semiconductor equipment vendors. These suppliers are often large enough to have their own proprietary platforms and control systems, and to offer process as well as equipment support, yet they’re small enough to offer the customization required to meet the unique needs of each manufacturer.
The entire laser bar manufacturing process flow needs to be optimized from end to end, including thin film deposition, to achieve the best end result. Thin films perform a number of critical functions within semiconductor diodes, ranging from forming the optical cavity to electrical and thermal transport. All of these directly relate to the performance and reliability of the lasers.
There is a tendency among process engineers to focus on specifying the production tool attributes they think are critical, rather than on specifying the system performance directly. But, it is possible to leverage industry-wide knowledge of system performance without losing control of tightly-held process knowledge. This approach will help engineers achieve optimal system performance by looking closely at requirements.
- Product performance is impacted by intrinsic film properties such as reflectivity, absorption, scattering and laser damage threshold.
- System performance, then is impacted by extrinsic properties such as uniformity, repeatability, deposition rate and throughput.
While optimizing each film individually may not yield optimum performance, choosing a tool that has been optimized for a specific function (rather than specifying a “bucket of hardware”) lets the vendor leverage their broad industry knowledge while allowing the manufacturer to maintain their own confidential process knowledge and minimize the acquisition and commissioning time.
When specifying a thin film system, do you often find yourself focused on tool attributes instead of system performance? Watch our webinar “Considerations for Thin Film Deposition in Semiconductor Laser Manufacturing” to learn how you can better support your entire semiconductor laser manufacturing process flow, from resistors and metallization to laser facets.
Watch On-Demand Webinar