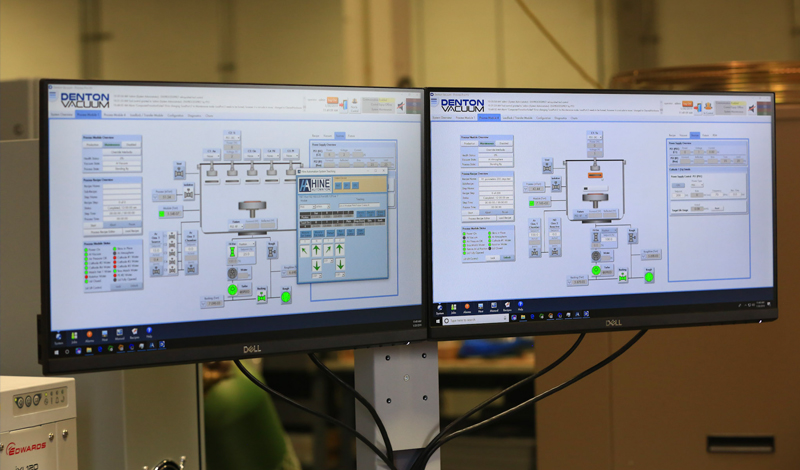
Posted on
In any thin film deposition process, software is required to run the system and record data from each run. Software also helps process engineers monitor feedback from in-situ controls and make other adjustments inside the system during deposition.
But not all deposition equipment software is scalable for high-volume production. More basic software is perfectly suitable for simple deposition processes and low-volume applications. For the best process performance, though, you’ll need a sophisticated software program specifically designed for automation to support high-volume production.
Checklist for Thin Film Deposition Software in High-Volume Manufacturing
Recipe manager: One of the most crucial components of the thin film deposition process is recipe building. This is where you specify the process steps that your wafer or substrate will go through as it gets coated. Some recipes are simple, but some require many process steps, with a wafer going through multiple chambers and receiving multiple layers. With a recipe manager, you can automate the process by identifying the setpoints and specs to hit for each step. The software will move the wafer from step to step based on time elapsed, pressure setpoints, and more.
Automated material scheduler: Based on your recipe, the material scheduler will identify the fastest, most efficient way to move each wafer through a multi-chamber configuration. The scheduler tells the robotic arm in a cluster tool which wafer to select next, where to move it throughout the process, and in which cassette slot to return it once it’s fully coated. It identifies and executes the most effective schedule for maximizing system uptime and efficiency.
Data logging and on-tool charting: For the best process control and to enable process improvements, your software needs to provide data logging and customizable charting. Your software should allow you to customize data views to your liking, and open as many at a time as you need without slowing down the system at all.
Diagnostics and troubleshooting: Your software should be able to run diagnostics either on-site or remotely, providing secure access to your supplier’s service team. This helps quickly identify and resolve issues, improving overall reliability and increasing system uptime.
Scalability across multiple applications: In the semiconductor industry, standardized configurations offer support for demanding, high-volume applications while also scaling down easily for lower production requirements. Even if you’re in a different industry, you can still learn from the compound semi world to benefit from software that can efficiently carry out process steps regardless of manufacturing requirements.