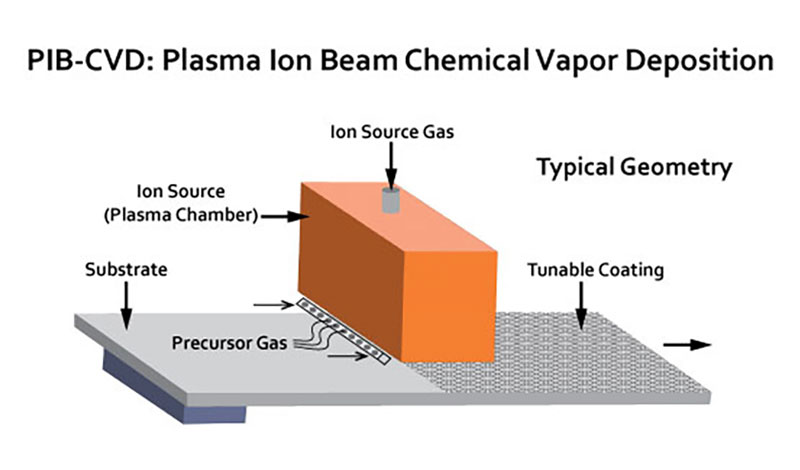
Posted on
In thin films obtained by Chemical Vapor Deposition (CVD), chemical reactions are driven by applying heat to the substrate to be coated or to the area immediately around the substrate. Reactive precursor gasses are then introduced into the deposition chamber and react immediately with the heated substrate surface or combine to form new compounds that grow films on the substrate surface.
Using plasma as an energy source allows CVD reactions to occur at much lower temperatures, avoiding the need to heat the substrate to such a high degree. Standard CVD temperatures are usually conducted at 600°C to 800°C, but with plasma – a high-energy stream of ionized molecules – CVD temperatures can range from room temperature to 350°C.
In this article we will compare two forms of CVD that utilize plasma: Plasma Enhanced CVD (PECVD) and Plasma Ion Beam CVD (PIB-CVD).
Plasma Enhanced Lowers CVD Temperatures
Plasma Enhanced Chemical Vapor Deposition (PECVD), also referred to as Plasma Assisted Chemical Vapor Deposition (PACVD), can produce unique compounds and films that cannot be created by common CVD techniques alone. It enables substrates to be coated at lower temperatures with less stress to the thin film interfaces, and it can produce films that demonstrate a very high solvent and corrosion resistance with chemical and thermal stability.
PECVD is usually performed in a vacuum chamber at pressure less than 0.1 Torr, allowing for relatively low substrate temperatures.
The primary advantages of PECVD over conventional CVD:
- Lower deposition temperatures
- Good conformity and step coverage on uneven surfaces
- Stronger bonding
- Tighter control of the thin film process
- High deposition rates
PECVD’s temperature range (200°C to 400°C) enables thin film applications in situations where higher CVD temperatures would damage the substrate. By operating at a lower temperature, less stress is created between thin film layers that have different coefficients of thermal expansion and contraction. This allows for good adhesion and high-efficiency electrical performance.
Plasma Ion Beam CVD Enables More Applications
Plasma Ion Beam Chemical Vapor Deposition (PIB-CVD) provides the same benefits as PECVD, and it takes plasma assisted deposition even further. This revolutionary thin film deposition technology provides a wide range of tunability, scalability, and durability. In PIB-CVD, the ion current density and the ion energy can both be independently controlled without the need for substrate biasing or additional grids. This provides the tunability to deposit materials with a wide range of properties even with a single precursor, enabling deposition of completely different films by simply changing ion source parameters. Since PIB-CVD also operates at room temperature, it has very low deposition temperatures that avoid damaging sensitive substrates.
Plasma Ion Beam CVD enables a variety of applications in a wide range of industries from semiconductor, to automotive, to roll-to-roll coating, to display manufacturing. PIB-CVD can be used to coat plastic surfaces that require properties like enhanced durability, high hardness, and low friction without the need of a wet chemical hard coat as the adhesion layer, making it useful for automotive applications. It can also be used to apply moisture barrier films and protective hydrophilic coatings for OLED encapsulation and large area optical coating. PIB-CVD allows for high-volume and continuous production of coated materials on a flexible substrate, so it can be used in roll-to-roll coating in applications such as printing, flexible electronics, and manufacturing of flexible packaging materials. The PIB-CVD technology can be used to deposit interlayer dielectric films that electrically isolate different metal layers and provide a planarizing layer for the subsequent metal deposition.
Benefits of PIB-CVD over PE-CVD:
- Highly tunable, with independent control of both the ion energy and ion current density, enabling a wide range of film properties including flowable, soft, thin film encapsulation layers as well as hard, highly hydrophobic, and optically clear coatings
- No need for substrate biasing
- Low-temperature process (room temperature, with no need for heat) for fabrication of electronic devices and plastic displays that would be damaged with higher temperatures
- Multilayer and gradient coatings can be produced in a single chamber from a single source, including inorganic and organic layers
- Performs large area coatings on both flat and curved substrates
- Ion source is easy to maintain, eliminating need for frequent maintenance
Large Area Coatings Made Possible with Phoenix
The Denton Vacuum Phoenix systems for PIB-CVD are high volume large area systems configured for in-line production to support high throughput for large volume production. The Phoenix is designed for easy maintenance and can be extended to include multiple sources. Learn more on the Phoenix PIB-CVD page.