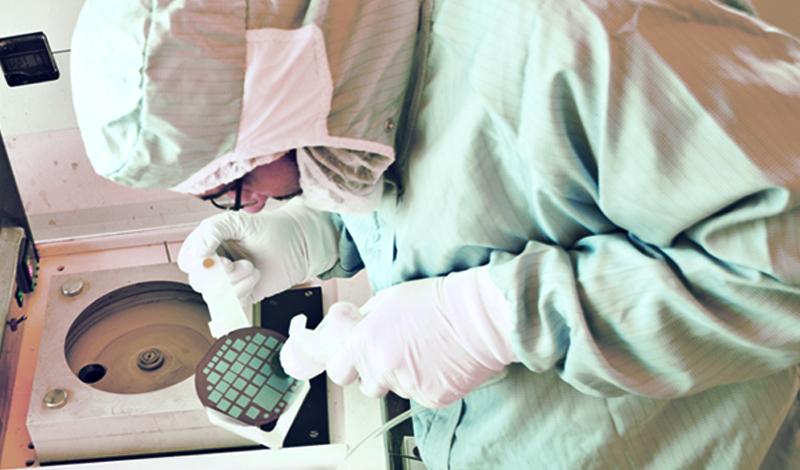
Posted on
For certain thin film coatings and applications, the substrate needs to be pre-cleaned inside the vacuum chamber in order to achieve desired properties and fulfill performance requirements. There are several methods that can be used to carry out this process, which have their own specific benefits depending on what you’re trying to achieve with pre-cleaning.
Benefits of Pre-Cleaning
Pre-cleaning removes water molecules, hydrocarbons and other particles or contaminants from a substrate before the thin film coating is actually deposited. It can also remove cross contamination from previous deposition steps. This process greatly improves adhesion to the substrate, leading to better performance and reliability for the coating. Better adhesion is particularly important for high stress films, since they will tend to peel off and impact yield and reliability. Improving both factors is especially beneficial for lowering your cost of ownership for high-volume production systems.
Pre-cleaning improves the thin film’s optical or electrical properties as well, which may be adversely affected by the contaminants. For the best performance, optics require very precise thin film specs to be hit. Any kind of surface contaminant can cause inconsistencies in uniformity and density, and will degrade qualities such as transmission and reflectance.
Certain pre-cleaning methods may also be used to micro-roughen the substrate, or to chemically activate the surface, which can improve adhesion in oxide films. The pre-clean method you choose will depend on what you’re trying to achieve or remove from the substrate.
Removal of an oxide layer requires an energetic ion source. Energetic ions will physically sputter etch the oxide layer. Typically, a gridded ion source is specified due to the high-energy (100s of eV) ions needed to remove the oxide layer. Etch rates are dependent on several factors: ion energy, ion flux, distance and angle of the ion source relative to the substrate.
Pre-Cleaning Methods
There are several different approaches you can take to pre-cleaning. Certain technologies, such as RF glow plates, are of a much lower energy than others. These methods are typically less cost-prohibitive and are usually a good option for simple pre-cleans, like removing hydrocarbons or moisture. They are also useful for delicate substrates that can easily be damaged by higher energy processes. However, for more difficult pre-cleaning processes on durable substrates where entire layers are being removed, a higher energy option is usually needed.
The different technologies used for pre-cleaning include:
- RF glow plate, which features low ion energies, covers a large area and has a low probability of damaging the surface
- Gridded ion source, which features high energy ions and a high-impact plasma pre-treatment. A gridded ion source is preferred for an oxide etch.
- Gridless end-hall ion source, which has a broad range of ion energies and a moderate to aggressive pre-clean. It is not an effective source for an oxide etch.
- Plasma pre-treater, which features a high voltage and high energy ion bombardment, and may require active substrate cooling
- RF or microwave plasma pre-treater, which features a low energy and moderate density plasma cleaning and is primarily used for a chemical surface pre-clean
Considerations for Choosing a Pre-Cleaning Method
Before you decide on a specific technology for pre-cleaning, there are certain performance, process and budgetary factors you need to consider.
- Deposition method: Your deposition method of choice will greatly affect your choice in pre-cleaning method. Ion source technologies are directly compatible with evaporation systems, but not so easily with sputtering systems.
- Depth of cleaning needed: You’ll need to consider exactly what you need to be removed from the surface of the substrate. If you’re simply removing hydrocarbons and water molecules, a method providing low ion energy should be sufficient. For removing entire oxide layers, you’ll need an approach that offers higher density and ion energy.
- Coverage area: The coverage area also varies between approaches. The RF glow pate and plasma pre-treater methods can cover large areas, whereas the RF or microwave pre-treaters and circular ion sources offer more limited coverage.
- Surface sensitivity: Depending on how sensitive your substrate material is, you could be at risk of damaging the surface through certain approaches. Typically, the higher energy, higher density methods are more susceptible to surface damage.
- Cost and complexity: It’s critical to understand all of the above considerations for your application before investing in a specific pre-clean approach. If your application does not require a high-energy or high-density pre-clean, then it will help you optimize your process and lower costs to go with a lower energy approach. And if you choose a method on performance alone, such as an ion source, without considering surface sensitivity, it could actually lower your yield and you won’t see any process benefits at all.
To learn more about pre-cleaning options for your application, contact the Denton team.