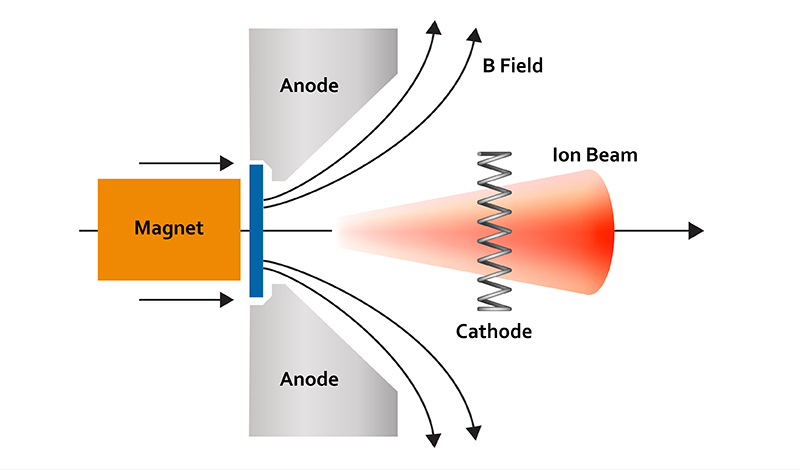
Posted on
Ion sources can be used in a number of deposition methods, including ion assisted deposition and ion beam sputtering. Your deposition method of choice may depend on a number of production and cost factors, but your ion source will have its own requirements based on your desired specs and application needs.
How Ion Sources Help During Thin Film Deposition
It’s important to understand exactly what you aim to achieve by configuring your system with an ion source, so that you can make sure it has the features you need. Ion sources have a number of benefits in terms of thin film specs and process upgrades:
- Adhesion and stress control: Ion sources have excellent pre-clean capabilities. If your application requires thin film coatings with good adhesion and tight stress control, you can use an ion source for pre-cleaning. Pre-cleaning removes moisture and any other surface contaminants which can lead to weaker adhesion and thin film performance.
- Improved thin film properties: Ion sources introduce energetic ions during the deposition process to produce fully oxidized films with higher density and less moisture absorption. They also help create “shift-free” thin films to boost performance.
- Process and manufacturing stability: By selecting the proper ion source, you assure a long, continuous operational time for your system, as well as run-to-run repeatability.
Types of Neutralizing Approaches
Depending on the process or thin film characteristics your application requires, there are several different methods that can be used for neutralizing the electron beam in your ion source.
- Filament: For shorter coating runs, an ion source that uses a filament as a neutralizing method may be a good solution. Tungsten is a common element used in filaments and can last for coating runs up to 10 hours. They are more cost effective for less demanding applications, and are suitable for performance when producing Vis/IR optical coatings or in metallization.
- Hollow cathode: Hollow cathodes have a much longer lifespan than filaments, delivering higher uptime and longer run times. They are more costly, but if you have higher manufacturing volume needs or need to ensure a high uptime, they are a good solution.
- Self-neutralizing: Ion sources that can neutralize themselves do not need a filament or cathode, which reduces the chances of contamination and also improves the uptime of your tool. You’ll gain independent control of current and energy to produce exact ion species for better process stability.
For more information on how the right ion source from Denton can help you address thin film deposition process needs, submit our contact form.