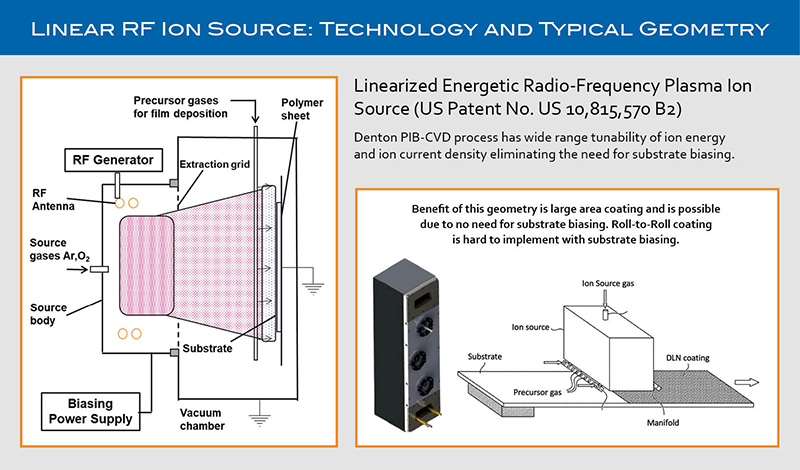
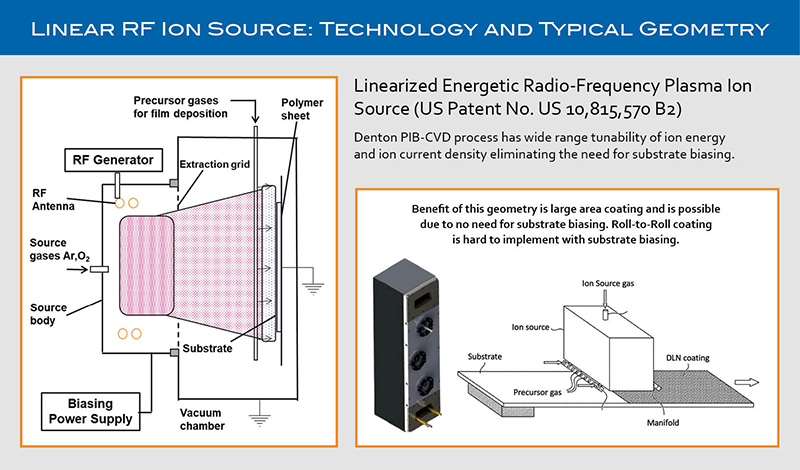
Why PIB-CVD? Process Tunability
Posted on
The Process Tunability of PIB-CVD Makes it Optimal for Many Thin film Applications. The inherent tunability of PIB-CVD enables a wide range of film properties including flowable, soft, thin film encapsulation layers as well as hard, highly hydrophobic, and optically clear coatings. As a result, multilayer and gradient coatings can be produced in a single chamber from… Read More